Transformation and digitalisation
In 2022, the KMG Corporate Centre underwent structural changes with a focus on advancing digitalisation. The Information Technology Department and the Transformation and Digitalisation Department were consolidated into the Digital Development Department.
During the reporting period, progress was made to implement digital initiatives across the Company’s core business areas. In particular, as part of the key project to digitalise oil production, Development of the ABAI Information System, two new modules were put into operation to tackle specific production issues. The Reservoir Fluids module introduced at Kazakhoil Aktobe supports the automated collection, interpretation and substantiation of oil reservoir fluid properties for accurate reserves estimation and field development engineering.
The Economics module launched at the KMG Corporate Centre serves to estimate the total value of assets of oil producing companies or the value of their individual existing fields and to forecast operating performance under various scenarios.
Earlier, five pilot ABAI information system modules were put into operation and proved to be highly effective: ABAI Database, Visualisation Centre, Well Operation Mode, Monitoring of Process Complications and Selection of Downhole Pumping Equipment. The Well Operation Mode module launched at Kazgermunai analyses the performance and calculates the production potential of wells, thus ensuring more efficient distribution of planned oil production among wells and reservoirs and optimising field development. It now takes the module only six hours to complete these operations instead of the five days previously required for human experts. Data accuracy went up from 85% to 95%.
A total of seven system modules are currently in operation. Ten more modules are planned to be introduced by the end of 2024 with a view to streamlining exploration, drilling, field operation, economic effect assessment and other processes.
2022 saw the continued development of the automated training system at KMG’s refineries based on computer simulators. Those are used to simulate routine operations and failures of the refineries’ process units. Thanks to the use of simulators, operators can practice production management in a virtual environment, which helps eliminate disruptions caused by human error and improve real-life safety.
In the reporting period, Pavlodar Refinery introduced computer simulators for the electrostatic desalting, dehydrating and atmospheric distillation units (EDD-ADU), naphtha hydrotreaters, catalytic reformers and gas fractionation units of the LK-6U complex. Going further, the project will be rolled out to cover the vacuum distillation (VDU), vacuum gasoil hydrotreating, catalytic cracking, absorption and gas fractionation units of the KT-1 complex.
Atyrau Refinery is expected to complete the introduction of computer simulators at EDD-ADU-2 and EDD-VDU-3 in 2023. The possibility of using simulators for petrol hydrotreaters (KU GBD and DT KU GBD units) is being assessed.
Overall, computer simulators are planned to be introduced for 13 process units of Atyrau Refinery, 9 process units of Pavlodar Refinery, and 1 process unit of PetroKazakhstan Oil Products.
In 2022, the initiative to implement a project management system (PMS) – viewed as key to business efficiency – was completed as part of the digital transformation, moving into the operational stage. The role of the business process owner was assigned to the newly established Project Management Office within the Company’s Strategy and Portfolio Management Department.
The system is based upon the phased implementation of all projects (assessment – selection – scoping – implementation – operation). At each of the stages, a comprehensive feasibility study is carried out to determine whether the project shall proceed to the next stage. Today, the Company runs all its capital projects in line with the phased implementation process.
The PMS defines the project management bodies and their relationship to one another, and classifies the types of decisions reserved to these bodies. It also defines the structure, main roles and functions of project participants, requirements for the structure and content of project documents, and guidelines on the use of project management tools. A methodology setting out the principles for recruiting, screening and engaging project team members is in place. It has already been used to set up project teams for the Tazalyq, Turgai Paleozoic and Urikhtau projects, a new gas processing plant in Zhanaozen, the Kenderli desalination plant and other projects.
A project management information system has been developed as part of the PMS. It provides prompt access to relevant project information (costs, deadlines, progress, etc.) for monitoring and timely management decision-making.
In developing the Company’s project management, a strong emphasis is placed on improving competencies and skills of involved employees. Centralised project management training has been provided since 2020, covering a total of over 2.000 employees of KMG and its subsidiaries and affiliates, including 70 managers. More than 30 employees have been certified according to the standards of the International Project Management Association (IPMA) and the Project Management Institute (PMI).
As far as operations are concerned, we will continue to build up the project management capabilities in the Company and its subsidiaries, provide methodological support, train employees, create a pool of project managers, develop and motivate project teams, and work in other PMS areas.
The newly established Digital Development Department will focus on developing/upgrading the IT and data management architecture to lay the ground for the Company’s digital development, as well as searching for industry-leading solutions in the areas of production, transportation and refining.
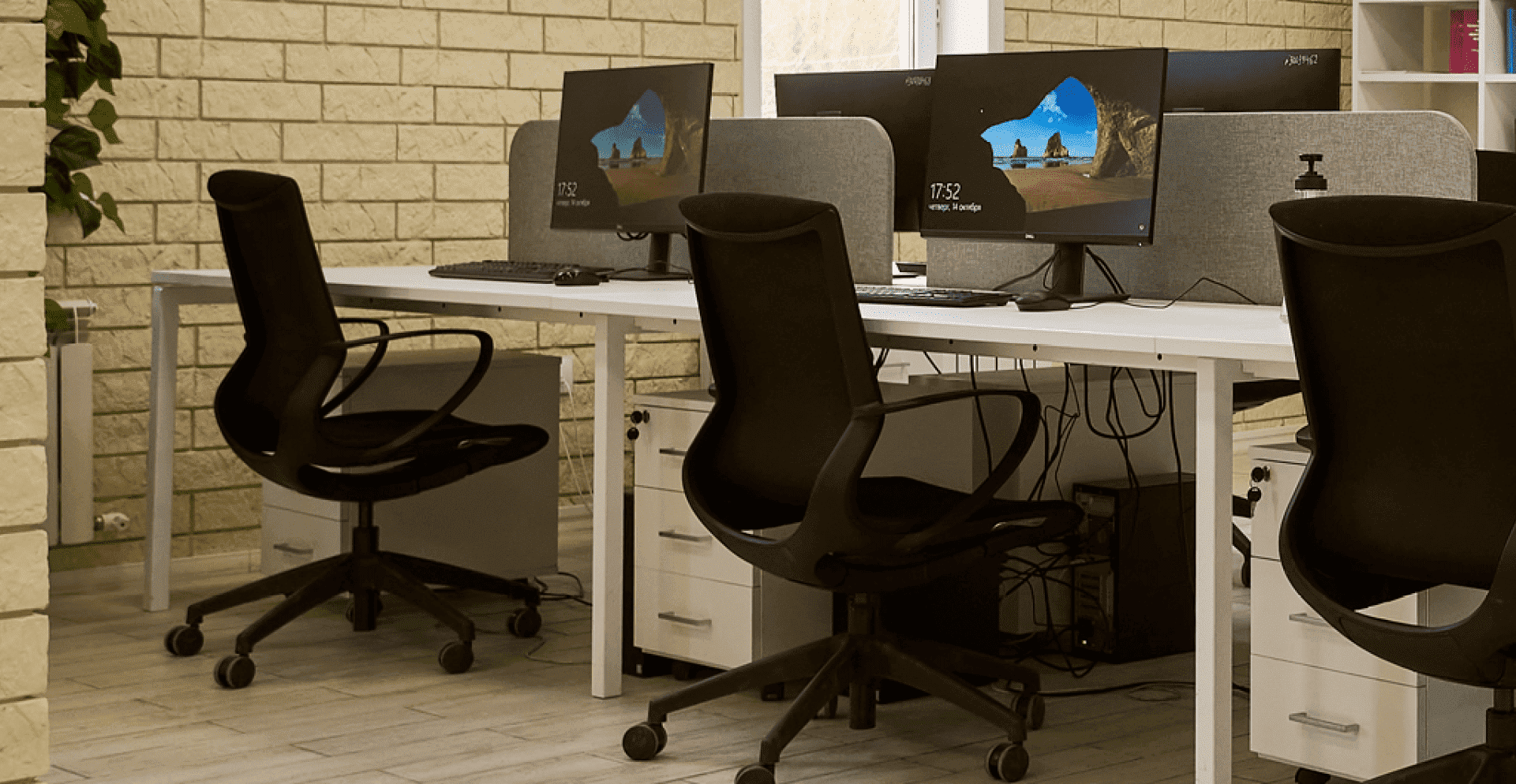